Timothy Wenhold is describing himself working in tandem with a robotic arm, “like the ones we use in manufacturing, but made smart and mobile.”
The description isn’t actually real for Wenhold— at least not yet—but it’s an appropriate scenario. Wenhold is the head of innovation at Power Home Remodeling Group, an industry giant with reported revenue of $540 million in 2017.
In this imagined future, Wenhold and the robot are installing a 300-pound bay window. “I’m on one side of the window, and the robot is on the other,” he says. It’s helping him lift, bearing a greater portion of the burden. The job is safer and less physically taxing. But that’s not all the robot is doing.
The average mason at Wilhelm Construction in Indianapolis lays, on a good day, 400 modular bricks. And then the company bought the SAM100, a semi-autonomous bricklaying robot with a self-contained energy supply and lasers and mapping software for efficiency and precision. SAM averages laying more than 2,000 bricks a day, the company claims. Its record is over 3,000.
Todd Berich, president of Berich Masonry, a Colorado-based company that operates mostly in commercial construction but also on the residential side, brought on a SAM100 near the beginning of this year. He says the impact of the robot, which he rents at around $20,000 a month, won’t be fully realized until about four to six months in, but already he sees the advantage. “The benefits are twofold,” he says. “We can do more volume, or in other words, say ‘yes’ to our clients more often. And already we’re seeing that people are thrilled with the quality SAM produces.”
“Most important is what I’m seeing in my heads-up display,” Wenhold says. “It’s helping to guide that whole assembly, sending me feedback about whether the window is level, how much force we need to move it forward, or whether we need to move it back. It makes the whole installation more precise.” It turns a three-man project into a one-man (and one “co-bot”) job.
Musings like that in industries like ours tend to trigger the same reaction: Sounds great for future me. Remodeling can’t stake the kind of investment necessary to support robotic construction. After all, it’s a highly fragmented field of mostly small companies. Typical remodelers just aren’t sitting on the type of throw-around capital necessary to employ robotics.
Trickle-Down Applications
Power is, though. And so is System Pavers, an outdoor living company with $100 million in revenue in 2017. Headed by futurist Larry Green, this year System Pavers brought on the company’s (and maybe the industry’s) first robotic employee. It’s a she, Green says, and she started in late May. Her name is Pepper. We’ll get to her later.
But real investment in robotics, at least on the consumer side, is coming from builders, mostly commercial but also residential. The technology, where it is right now, makes more sense for it.
For starters, building activities lend themselves to replication.
Take building a brick wall: you set your line, spread your mortar, lay your course, and repeat. It’s basically 3D printing but with humans (as future kids will say). Australian company FastBrick Robotics will soon bring to market its loudly anticipated Hadrian X bricklaying robot, which the company colors as “revolutionary.” The bot is a reimagining of bricklaying as a manufacturing process, where the human component is reduced to loading bricks onto the machine’s conveyer belt. The Hadrian X can spread mortar, lay the courses, fill the voids, cut and reshape bricks, and understand CAD designs for absolute precision; its 92-foot, robotic arm-tipped boom is dexterous enough to leave customized spaces for wiring and plumbing. The machine is one in a growing generation of worker bots.
A building engineering company out of the U.K., Newtecnic uses 3D BIM modeling to develop highly complex designs, like the façade on the King Abdullah Financial District Metro building in Riyadh, Saudi Arabia. It’s 650 feet of twisting, curving concrete composite panels, held together by a modular system that relies on adjustable steel spider fixings. Visually, the exterior is meant to mimic desert wind, but it’s also designed to reduce solar gain and, as if an homage to its design-sake, create air currents, which help cool the building. True to Newtecnic’s reputation as a forward-thinking company, the KAFD hub also incorporates an expectation of the future into its designs—the constant presence of robots. In an interview with Construction Global, Newtecnic founder and CEO Andrew Watts said that the company’s designs assume robots and drones will be able to inspect the building and use on-site 3D printers to manufacture repair parts as needed. Currently, cranes do that work, but Watts says it’s only temporary. “Panels will become steps for [robots and co-bots] to climb up and access the fixing points at each successive step of the installation as structure becomes more geared to the interplay between our machine colleagues and the building.”
Construction Robotics out of New York has its own bricklaying bot called SAM100, which is already on the market and with at least one early adopter boasting claims of a 400-plus-percent productivity boost. Construction Robotics is soon to release a second lift-assistance bot called MULE. Caterpillar has a whole line of construction vehicles fitted with various levels of automation, from self-driving trucks to excavators that can benchmark and hammer transits without a second man. Brokk, a manufacturer based in Monroe, Wash., makes demolition arms than can be remotely instructed to plow through most any wall. And London-based building engineering company Newtecnic is so confident in the inevitability of applied robotics in construction that its designing buildings with the expectation that robots will administer future maintenance.
But those are for big builders. “It’s almost like they moved manufacturing into the field,” says Power CIO Wenhold. “Saves money and helps efficiency, nothing wrong with that. But it’s not intelligent.”
Yes, you could use a demolition bot to knock out an exterior wall, but there’s not much room for a tool that weighs enough to buckle floorboards, or won’t fit through the front door. The Hadrian X can’t install a bathroom vent, or do a concrete stair retrofit. Where are the window-installing bots? Where are the framing bots? (Full disclosure: MIT’s Computer Science and Artificial Intelligence Laboratory has a robot in development called the AutoSaw, which largely automates the use of a chop saw and jigsaw to make furniture.)
The AutoSaw was created with safety specifically in mind. “If you’re building a deck, you have to cut large sections of lumber to length, and that’s often done on site,” stated Jeffrey Lipton, the lead author on the first paper describing the system. “Every time you put a hand near a blade, you’re at risk. To avoid that, we’ve largely automated the process using a chop-saw and jigsaw.” The machine is unique in that it uses AI to increase customization in its carpentry. Right now the AutoSaw is seen as a tool for furniture making. But its versatility speaks of great potential to come. “Systems that can work in unstructured physical environments, such as this carpentry system, are notoriously difficult to make,” Hod Lipson, a Columbia University professor of engineering and data science said in a statement. “This is truly a fascinating step forward.” It’s easy to see how the technology could translate to cutting lumber for remodelers.
That distinction is an important one, because it marks the divide between what construction robots are, and what remodelers ultimately need them to be: efficient, responsive helpers.
Recall Wenhold’s vision of the future: the window installation that had man in tandem with machine. In that scenario, what makes the co-bot, as Wenhold called it, truly valuable, isn’t its power to lift, which can be achieved using a simple machine. The value is the telemetries the co-bot was feeding him, and its ability to interpret and respond in real time to that data, as well as him.
“The difference between these co-bots is that they’re aware and working with their human counterpart,” Wenhold says. “You think about something that isn’t in a simple pattern, like … replacing an opening that used to have a picture window and now we’re putting a big bay window. That’s a place where if we can’t find that cooperation, the bot isn’t going to be all that useful.”
Putting the Pieces Together
The thing is, Wenhold’s not a pie in the sky kind of guy. He’s a measured, experienced chief officer of one of the few residential remodeling companies you can unironically call a juggernaut.
And robotics aligns with his expectations of how the industry will develop. Yes, there is a disconnect between the tech available and what would be required for a robot to make its way onto a jobsite as eclectic and unpredictable as one you’d find in remodeling, but the co-bot of Wenhold’s future isn’t something he plucked from his imagination. “The parts are all there.”
Like YuMi, a relatively compact (83 pounds), dual-armed robot designed by ABB Robotics for small parts assembly (i.e. toys, watches, and the like). It’s built not to operate in a cage or in a taped-off section of a factory, but rather alongside other human assembly workers, doing the same work. It’s a collaborative bot, the company calls it, relying on flexible hands, a vision system, and “sensitive force control feedback,” as well as “lead-through programming,” which translates basically to it ensures safe interaction between itself and those around it, and that it can be taught things.
YuMi shows off a lot of the hallmarks of Wenhold’s future co-bot, even if it costs $40,000 and is built for a factory setting. The underlying concepts (brought to fruition) are the important part.
As for the rest: You can find a heads-up display in Microsoft’s HoloLens—something already being incorporated into construction. And thanks to the economizing of basic computers, like Raspberry Pi, fastening, programming, and networking sensors for telemetry is quickly gaining a reputation as a Millennial pastime. “Someone just needs to put the pieces together,” Wenhold says.
And some day, maybe soon, some company will. In the meantime, the problems robotics offer solutions for remain problems. There are 250,000 unfilled construction jobs in the U.S., when a year ago there were only 159,000, according to consulting group McKinsey.
For Those Uninterested in Waiting
Made by SoftBank Robotics, Pepper (pictured right) is a humanoid robot designed for customer service, which is exactly how Green uses her. “She’s a little bit like a digital assistant,” he says, only way more functional. Pepper can identify people from up to 15 feet away and use size to differentiate between adults and children; so if a family of five comes into a showroom, she can offer to read the kids a story while the parents talk with a sales rep. She can engage clients, answer questions, entertain, and collect lead data. “The programmable features are unlimited,” Green says. “Pepper could give an entire sales pitch, if we wanted her to.”
To be clear, there is no place for Pepper on the jobsite. But she’s going to save System Pavers money nonetheless. “Cost is one of the things that motivated us to buy Pepper,” Green explains. “Over a 36-month period, assuming a 40-hour work week, Pepper will end up costing us seven dollars per hour.”
But framing Pepper as a human analog isn’t the message Green hopes his new hire will convey. He uses a book to make his point: What To Do When Machines Do Everything, written by the trio of Malcolm Frank, Paul Roehrig, and Ben Pring, all futurists and technology executives. “The book makes the case that robots aren’t going to replace jobs.” For some jobs they will, he admits, but only ones that are low-level. Like the way a nail gun removed the job of swinging, the purpose is to improve performance. “We’re not worried about losing jobs,” Green says. “It’s the problems like labor and productivity that’s forcing these innovations to begin with.”
It brings us back to Wenhold’s co-bot. “Even if I originally needed three people to lift that 300-pound window, they were only working on that for an hour or so. The machine would allow those two additional workers to start on another part of the project,” Wenhold explains. “What we’ve really done is added a super crew member to make everyone else more efficient. What used to take six hours would take four, which would mean two jobs in a day instead of one.”
And yeah, that may be a futuristic way of looking at it, but in many respects, we’re already heading into that future.
About the Author
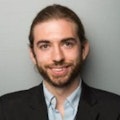
James F. McClister
James McClister is managing editor for Professional Remodeler.