One of the biggest concerns in residential construction is selecting windows that won’t degrade over time. The folks at Andersen Windows & Doors met this challenge head-on with a remarkable and innovative manufacturing approach. We asked Brandon Berg, Andersen’s senior vice president of research, development and innovation (RDI), quality and sustainability, about this solution.
Berg is a member of Andersen’s executive committee and has been with the company since 2011; he holds a B.S. degree in chemical engineering. During his tenure at Andersen, he has overseen research and development, quality assurance and lean six sigma, as well as material technology and testing.
In the Q&A session below, we asked Berg about Andersen’s unique Fibrex® material, how it’s made and the benefits it offers to homeowners.
What were the challenges that first led to Andersen’s development of Fibrex® material?
A big issue we saw in window construction had to do with windows that rot, blister, peel and need to be repainted — and eventually replaced. These are issues often seen with vinyl and we were looking for a better alternative.
Vinyl is popular for a couple of reasons though. First, it’s water-resistant, and second, it’s relatively inexpensive. But vinyl isn’t optimally durable, and black and dark brown vinyl windows are especially problematic due to their color — they tend to absorb more heat, which makes them particularly prone to warping. That of course leads to air intrusion and even water leaks over time.
We wanted to develop a material to capture the benefits of vinyl but also take its properties to the next level, making it more durable and maintenance-free, while also being more sustainable. That was what inspired the creation of Fibrex.
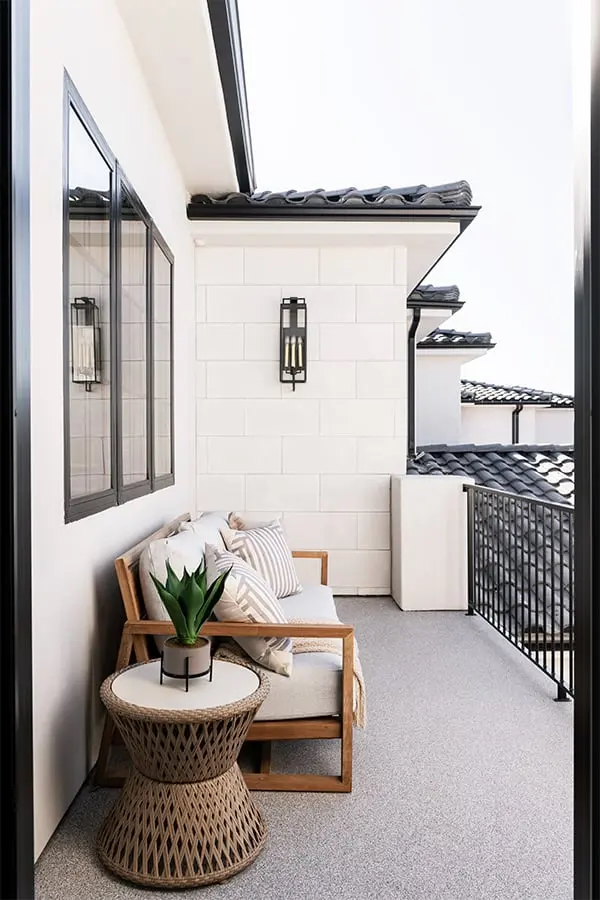
So what’s Fibrex made of and how is it manufactured?
Something we were mindful of is how much scrap wood fiber we ended up with after making traditional wood window frames. We decided to reclaim that material and blend it with a polymer. Fibrex is actually 40 percent wood fiber by weight, with the rest being thermoplastic polymer — and some of that material is also reclaimed. We heat up the wood fiber to remove the moisture, then add it to the heated polymer material.
What happens next is pretty remarkable — the wood molecules bond with the polymer to create a brand new material. When the mixture is pressurized, the polymer fills up and coats the cells of the wood fibers and they align, binding together to form a strong and durable — yet water resistant — material. The compound is then extruded into the desired shape with the color permanently applied. That’s Fibrex.
How is Fibrex superior to other types of windows?
It never needs painting, which is a real boon to the homeowner. And it doesn’t rot, fade, blister or peel the way vinyl does. Click here to view individual product warranties for more information. We’re so confident that Fibrex windows won’t lose their color over time that we offer a fade warranty. In addition, Fibrex is twice as strong as vinyl, and it won’t bow or warp, no matter what climate the home happens to be in.
If black or dark-colored windows are part of the home’s design, the economical Andersen 100 Series offers Fibrex frames with that option.
This is a game-changer. In fact, this manufacturing process is so innovative, Andersen has more than 30 patents for it.
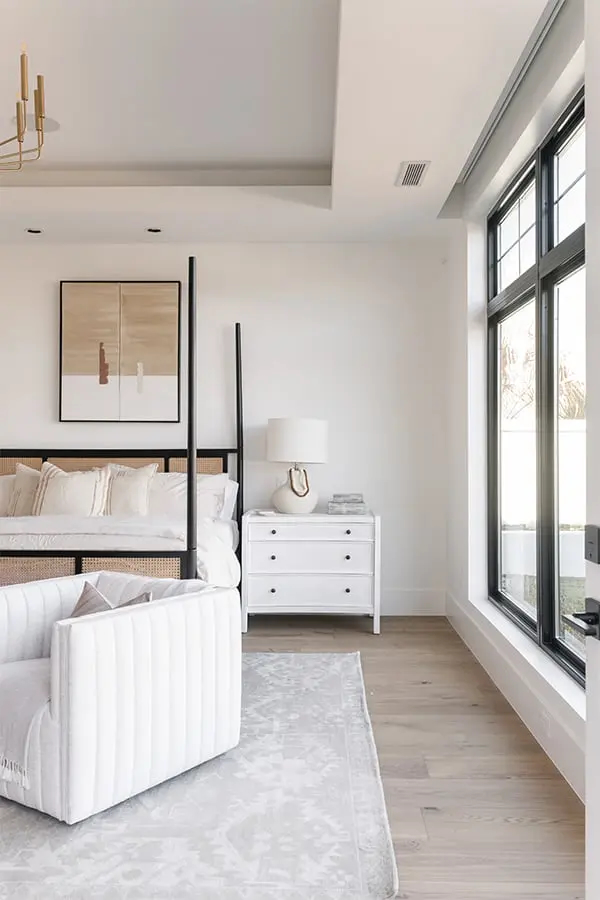
What’s the takeaway for those considering Fibrex windows for their building projects?
Simply put, Fibrex windows offer their customers, the homeowners, budget-friendly visual appeal and incredibly durable performance. Over time, they’ll truly appreciate how maintenance-free these windows are, relieving them from worrying about restoring or replacing them and the associated expense, regardless of how hot or cold it is where they live. And in addition to their climate-resistance and stylish design, they’re made with sustainability in mind. That’s hard to beat.
For more information, visit andersenwindows.com.